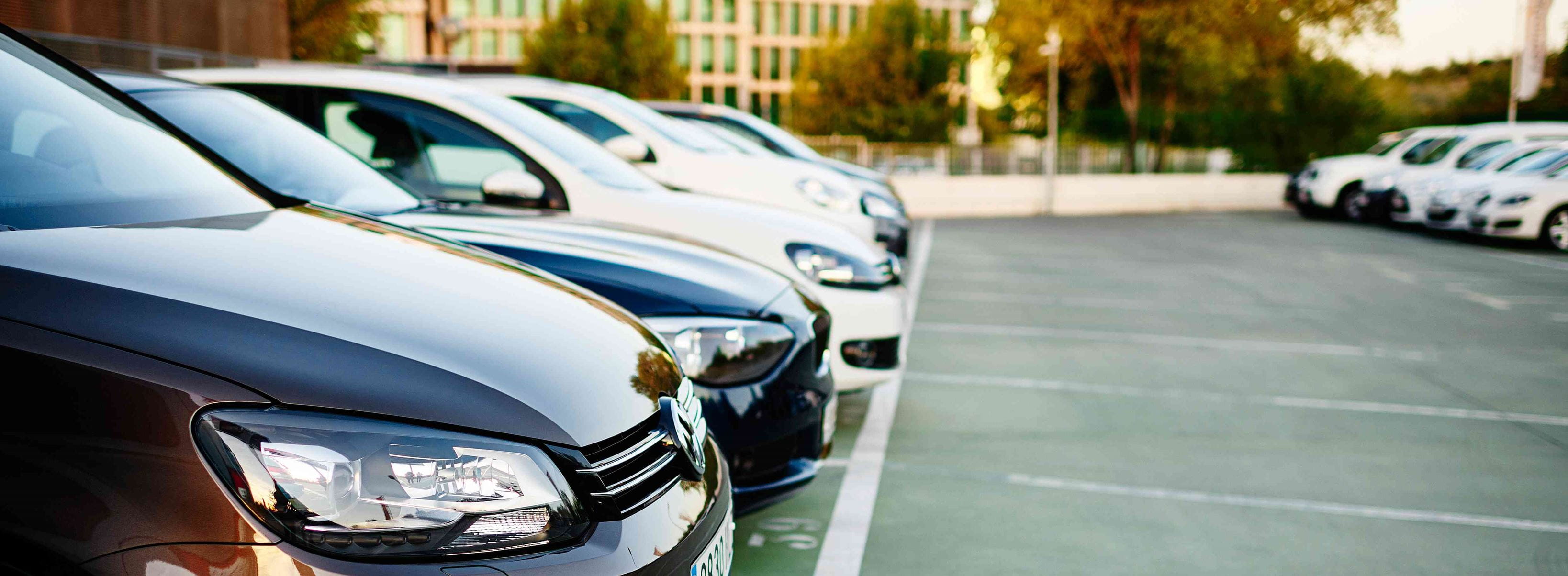
Why you need to wait longer for your new car and what to do about it
LeasePlan International and Roland Berger hosted a webinar on the semiconductor shortage and what fleet managers can do. Experts from both companies shared their insights on the overall macro situation and the impact of the semiconductor shortage in the automotive sector.
Managing a fleet can be difficult nowadays with the shortage of semiconductor chips resulting in longer lead times for new cars. With vehicle electrification and our growing digitalisational needs, we’ve created a different way of building cars. Cars used to be a mechanical device, but the car of today and tomorrow is a software-enabled and cloud- connected data device. Basically a smartphone on wheels. Run by an ingenious operating system which requires semiconductors (or simply said: chips). They enable most of the innovations in vehicle development.
What can fleet managers do?
Proactively anticipate delays in the ordering process
- Place orders as early as possible: 6 till 9 months earlier
- Accelerate the electrification of the fleet as OEMs are prioritising the production of low and zero emission vehicles
- Assess what equipment is needed when ordering a vehicle
- Explore widening the scope of OEMs on the company car policy
Production lead times are still increasing in 2021
Keep an eye on availability. This may mean that vehicles will not meet all the driver’s expectations, but at least cars are being produced.
- OEMs will continue to prioritise low and zero emission models
- Optional equipment with high “chip consumption” will see longer delays
- LCV availability will improve HY1 2022
- Increases in prices: Raw material prices are increasing (steel/aluminium), which may lead to price increases
When will lead times return to normal?
- Q4 2021 - improved chip availability (Taiwan)
- Q1-Q2 2022 - OEMs working through high orders banks
- Q3+ 2022 - new chip production facilities become operational
e.g. Bosch factory in Dresden Germany
- Q4 2022 - OEMs increasingly returning to normal lead times
- 2023 - Major new chip production facilities come on line
i.e Taiwan Semiconductor Manufacturing Company (TMSC)
Why is there a shortage?
To understand the bigger issue let’s zoom in. In short: the shortage is the result of the massive cancellation of chip orders by car manufacturers when demand for cars collapsed, mainly due to the covid crisis. As demand for new cars recovered faster than expected, automakers were left behind as global demand for chips had surged in the meantime.
But be aware that cars** account for less than 1% of all connected devices**, which is a direct disadvantage for the automotive industry.
Technology trends, new electronic architectures and supply disruptions require to redefine the view on the semiconductor supply chain
The semiconductor demands in most end-markets are driven by these global digital trends:
- 5G Internet of Things (IoT) (consumer and industrial)
- Artificial intelligence (AI)/big data
- Autonomous systems
- Cybersecurity
In 2025 there will be over 70 billionconnected IoT devices.
Couldn't we have seen it coming?
Well.. yes, but not as severe as it is now. In the automotive industry, on the demand side there is:
- Competition for capacity with next-gen electrical/electronic vehicle system architecture (E/E architecture)
- External shocks causing fluctuating demand: probably the most important is Covid
- Vehicle electrification – the amount of semiconductors in electric vehicles is rising
Where on the supply side there is:
- A competing demand and political risks
- Disruptions from external factors e.g. covid
- The semiconductor cycle time
This gap between the supply and demand has created the global semiconductor supply shortage.
The shortage is not only a result of the pandemic,** it is a combination of many factors faced in the last one and half years.** On the supply side there were difficulties in access: Covid is a major external shock but so was the blockage of the Suez channel or the Texas factories freeze.
The external issues weren't the only problem, there was a mismatch in the supply chain. For the automotive industry, the supply chain is more complex than it seems due to various production steps, business models and a large number of companies in the value chain. It takes at least 3 months to produce and ship a semiconductor chip, even if there is enough capacity!
Another complex factor is cost for developing. Advanced node chips (SoCs) are growing exponentially and repayment of the high development cost drives the need for high volumes. Only two companies are able to produce advanced leading node chips (and they are both in Asia). That is a significant risk, that policymakers are responding to by pushing re-localization of the semiconductor supply chain.
Localising semiconductor production
The United States, European Union and China are responding to this semiconductor shortage by rethinking the supply chain and attempting to re-localise production.
United States
- CHIPS act provides $52B of subsidies to domestic semiconductor manufacturing
- US government re-evaluates export controls and import restrictions of semiconductors
European Union
- $145B EU investment into semiconductor technologies
- Structured approach to address Europe's weaknesses in digital
- Three pillars for future policy: AI, data and industrial strategy –linked to different initiatives/investments
China
- National Semiconductor Plan to boost domestic semiconductor industry backed by extensive funding e.g.,:
- Made in China 2025– Direct state support champions (Huawei)
How are OEMs and Tier-1s responding to the shortage?
In fact there is no single solution. The shortage will last into 2022 and the lost production will be felt globally. We need to be aware that risk factors will always remain and reappear. OEMs and Tier-1s (chip suppliers that deal directly with OEMs) are mitigating the crisis across the near, medium and long-term time horizons. These are the strategic responses to the crisis:
1.Immediate repair; bear the risk (next 6-12 months)
- Supply chain transparency,
- Volume commitments,
- Flexible production schedules
2. Risk mitigation; source to risk (next 1-3 years)
- Advanced sourcing management
- Dedicated semiconductor teams & processes
- Inventory strategies
3. Fundamental change; design to risk (next 3-10 years)
- Component standardisation
- Volume bundling
- Next gen E/E architectures
We expect the challenges in the automotive semiconductor supply chain to persist so automotive players and Tier-1s need to be prepared.
The situation will continue but ultimately we will be able to go back to normal production levels. But only expect that from 2023.